Over-emphasis on the types of tools
It is easy to choose a machine with a variety of cutting tools, thinking that the more tools, the more versatile it is. However, too many types of tools often complicate machine operation, increase maintenance costs, and may cause unnecessary complexity. Too many options also make it more difficult to simplify the production process.
Ignore the matching of tool materials and cutting capabilities
Many consumers ignore the matching of cutting materials and tools when choosing CNC oscillating knife cutting machines. Different tool designs are suitable for different types of materials, such as paper, plastic, leather, cloth, etc. Consumers tend to think that one tool is suitable for all materials, but in fact, the hardness, material and design of the tool affect the cutting effect, speed and accuracy. If the tool is not suitable for the material, it may cause uneven cutting, damage the tool, and even affect the quality of the product. Therefore, it is crucial to choose a tool suitable for a specific material.
Our advice:
Focus on tools that match the materials and processes you use most often. You don’t need all possible tools – just tools that meet your specific cutting needs. Simplify wiring and operation: Machines with too many tools also increase wiring complexity, making electrical problems more likely. In addition, overly complex machines require a longer learning curve, making it more difficult for operators to quickly master the machine.
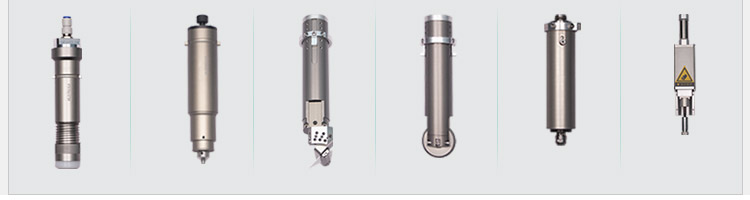
Emphasis on large cutting surface
Customers often believe that the larger the cutting area, the more efficient the machine. While larger machines may be beneficial for mass production, they lead to increased costs, a larger machine footprint, and transportation challenges.
Underestimating the working stability and accuracy of the machine
Some consumers also pay too much attention to price when purchasing CNC vibration knife cutting machines, ignoring the working stability and cutting accuracy of the machine. Cutting accuracy is a key factor affecting production efficiency and product quality, and cheaper machines may perform poorly in these aspects, resulting in increased cutting errors or decreased accuracy after long-term use. It is recommended that consumers pay attention to the brand, reputation, and customer feedback of the machine tool when choosing, and ensure that its accuracy and stability meet their own production needs.
Our advice:
Match the machine size to your material size: Choose a machine with a cutting area that matches the size of your typical material or the largest part you need to cut.
Consider transportation and assembly issues: Machines with a width of more than 2280 mm need to be assembled for transportation, which increases complexity and installation challenges. A more appropriately sized machine can save transportation costs and reduce assembly time. Understand the impact on accuracy: Larger machines usually require extension of the X/Y axis, which may affect precision and overall accuracy. Operating cost factor: Larger machines also require higher vacuum pump power, which increases operating costs. Choose a machine that fits your specific cutting needs to avoid unnecessary expenses.
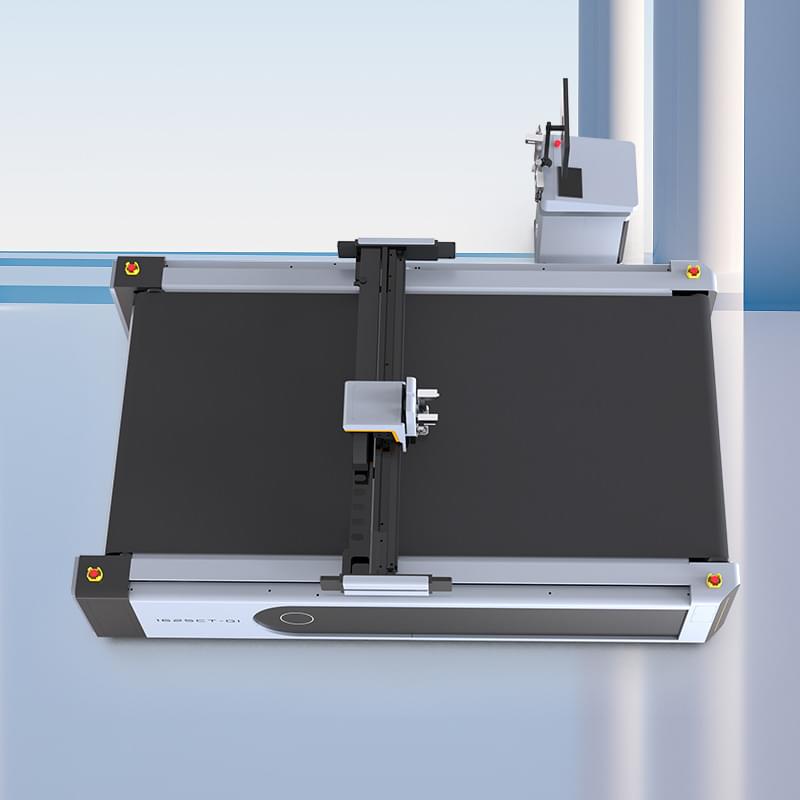
Go for a larger cutting height
Many customers assume that machines with the highest cutting heights are the most versatile. However, this is not always true, as not all applications require the maximum cutting height, and this feature can present its own set of challenges.
Our advice:
Choose a cutting height based on material thickness: Choose a cutting height that is appropriate for the thickness of the material you regularly work with, rather than simply choosing the highest height.
Consider maintenance and accuracy: Machines with larger cutting heights require a larger lifting mechanism, which increases maintenance costs and reduces cutting accuracy. The larger the lifting range, the greater the potential for problems during normal use.
Balance material versatility and accuracy: A cutting height that is too high may reduce the machine’s efficiency when cutting medium-thickness materials, as it may require a longer blade, which is more susceptible to damage and wear.
Ignoring the compatibility of software and hardware
The control system and software of the CNC vibration knife cutting machine are the core parts of its operation. Machines from different manufacturers may be equipped with different control systems or software platforms. Some consumers do not consider the compatibility of these systems and software when choosing, especially when they already have certain specific design software. If the software of the cutting machine is not compatible with the existing design system, it may increase the workload and difficulty of operation, and reduce production efficiency. Therefore, when purchasing, it is necessary to ensure that the software system of the selected equipment can be smoothly connected with the existing technical equipment and production processes.
Ignoring operation training and after-sales service
Many consumers only focus on the equipment itself when purchasing the machine, and ignore the importance of operation training and after-sales service. As a high-precision automation equipment, the operation and maintenance of the CNC vibration knife cutting machine requires professional technical support. Without sufficient operation training and perfect after-sales service, users may encounter difficulties during use or the equipment may not be solved in time when it fails. This may lead to production stagnation, increased maintenance costs and shortened equipment life. Therefore, it is particularly important to choose a manufacturer with good training and after-sales support.
Selecting the right oscillating knife cutter requires a careful assessment of your specific production needs. Avoiding these common mistakes can help you select a machine that is cost-effective and perfectly suited to your business.
Focus on what really matters: matching the machine’s capabilities to your materials, cutting needs, and operational requirements. By doing so, you can achieve maximum efficiency, reduce unnecessary costs, and extend the life of your investment.
AOL intelligent blade cutting machine has high precision and high efficiency. Our professional after-sales service can provide automatic cutting solutions for various industries.
For more information, please consult:
Email: [email protected]
Phone: +86-531-88620680
WhatsApp/We Chat: 0086-18560162709
youtube: https://www.youtube.com/channel/UCDiNQSjBR5DsAX9QfkWF7AA
Website: https://aollaser.net/